How To Weld Magnesium
February 09, 2023Welding magnesium alloys is tricky and requires many precautions and a thorough understanding of this material. However, once you prepare everything and choose a suitable welding process, welding magnesium becomes relatively straightforward.
Magnesium alloys with small amounts of aluminum, manganese, zirconium, zinc, and rare earth metals can have a strength that equals steel. But magnesium is exceptionally light. In fact, magnesium is four times lighter than steel and only two-thirds of aluminum's weight! This makes magnesium perfect for many machinery parts, the aerospace industry, and castings.

Magnesium repair
photo by @tig_happens
This article will teach you why welding magnesium is challenging, some VERY important safety measures, different magnesium alloys, how to prepare this material for welding, and which welding process to choose.
Challenges Of Welding Magnesium
Magnesium looks and feels a lot like aluminum, and welding magnesium shares many of the same challenges as welding aluminum . However, it's a big problem to mistake magnesium casting for aluminum casting. Welding magnesium with an aluminum filler metal will create an extremely weak joint and possibly ruin the part, which is a huge problem since these castings are usually expensive. So, the first challenge is figuring out if the part you need to weld is magnesium or aluminum.
You can use plain white vinegar to differentiate between aluminum and magnesium alloys. Just pouring a few drops on a clean metal surface will tell you which material it is from — magnesium will cause vinegar to start foaming up, while aluminum will have no reaction.
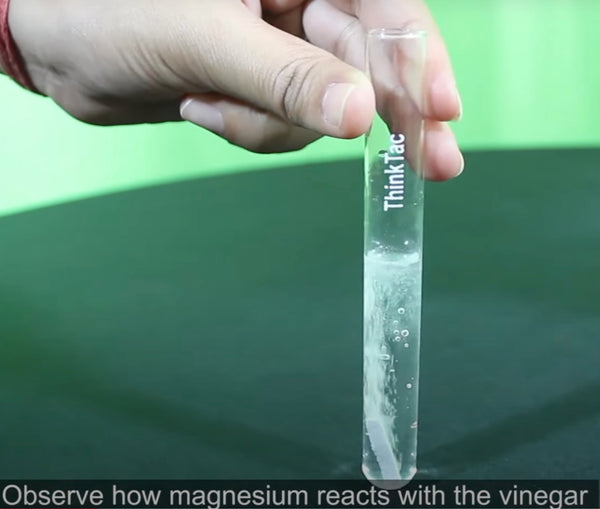
Source: https://www.youtube.com/watch?v=RSrepYVCwD0
While this is a different metal, welding magnesium is much like welding aluminum. So, if you welded aluminum before, you'll have a higher chance of repairing magnesium castings.
Magnesium reacts with oxygen and creates a magnesium oxide on its surface, just like aluminum. This oxide must be removed before welding because it has a higher melting temperature. So if you don't remove the oxide layer, it can get trapped in the weld as inclusions and weaken the joint.
Magnesium castings are often soaked in oil during their life cycle. Usually, shafts, bearings, gears, and other machinery parts are made from magnesium alloys. Once they break, it's often cheaper to repair them instead of buying a new part. Sometimes, these parts can cost up to 100,000 US dollars, making them very expensive to replace.
However, the oil gets soaked into the magnesium casting and gets logged deep into the casting pores. Since these machinery parts are exposed to high-temperature differences, the pores expand and contract and can trap oil deep beneath the surface. This can make welding magnesium parts quite challenging, depending on the oil intrusion severity.
Welding oil impregnated cast Magnesium. Fixed up a old Husqvarna 2100 chain cover.
Photo by @darrylrayk
There are many magnesium alloys, and your approach may be different with each. So, you can't always just jump the gun and weld any magnesium the same.
Magnesium has a very high thermal conductivity and expansion rate. Therefore you must use concentrated heat and account for the material's expansion. The joint or repair area shouldn't be constrained to prevent cracking.
In addition, the welding arc is obstructed by the zinc reaction in the puddle. It takes a lot of skill to weld magnesium because it requires a tight arc and won't give you a clear view of the arc at the same time. We recommend first becoming proficient with welding aluminum before you try welding magnesium.
Welding Magnesium Safety Measures
Many magnesium alloys have a high zinc content, making them particularly dangerous and challenging to weld. As you probably already know, zinc is a welder's nemesis. It's cancerogenic, and can cause severe health problems if inhaled in large quantities. So, ensure you wear a respirator, use appropriate ventilation, and abide by OSHA regulations for controlling hazardous fumes and welding gases .
Apart from zinc content, magnesium itself poses a huge safety risk. Magnesium is a HIGHLY flammable metal. It's so dangerous that once it catches fire, you CANNOT extinguish it with water or carbon dioxide! It can literally break molecular bonds of H2O, release individual atoms of hydrogen and oxygen, and use them as fuel! So, if it catches fire, pouring water would be as if you added gasoline to the fire!
However, the casting itself has a high volume and is less likely to catch fire. But, magnesium shavings and grinding dust absolutely can catch fire. So, be extra careful when welding magnesium and apply every standard welding fire safety practice, like keeping anything flammable far away from the work area. In addition, it's a good idea to sweep the area of any magnesium grinding dust before welding. This will prevent welding sparks from igniting magnesium shavings and dust.
Magnesium firestarter (in left hand), used with a pocket knife and flint to create sparks that ignite the shavings.
Source: https://en.wikipedia.org/wiki/Magnesium
Make sure you have a Class D OSHA recommended fire extinguisher on hand or a lot of sand. This is the only way to put out a magnesium fire because it burns at 4,000˚F! Extinguishers that are suitable for Class D fires should be identified by a five-point star containing the letter "D."
Weldability Of Magnesium Alloys
Magnesium is often combined with other materials to increase its strength and suitability for various applications. Some commonly used alloying elements include zinc, aluminum, manganese, zirconium, and rare earth metals.
The designation for these magnesium alloys often consists of one or two letters indicating the specific alloying elements, followed by the percentage of each element in the alloy. For example, the ASTM designation AZ91C indicates an alloy containing 9% aluminum and 1% zinc.
Source: https://www.accessengineeringlibrary.com/
Magnesium-aluminum-zinc alloys, such as AZ31B, AZ61A, AZ63A, AZ80A, AZ81A, AZ91, and AZ92A, may contain up to 10% aluminum to improve their weldability by refining the grain structure.
However, zinc content above 1% can increase the risk of weld cracking. Therefore, alloys with high zinc content, like ZH62A, ZK51A, ZK60A, and ZK61A, are not recommended for arc welding due to their susceptibility to cracking and poor weldability.
Magnesium containing small amounts of thorium has excellent welding properties and is resistant to cracking, and weldments made with these alloys do not require stress relieving.
On the other hand, certain magnesium alloys are prone to stress corrosion, and weldments used in corrosive environments may crack over time if residual stresses are not relieved through stress relieving.
Stress corrosion cracking caused by tension developed in an unsuitably welded reinforcement collar
Source: https://en.wikipedia.org/wiki/Stress_corrosion_cracking
Preparing Magnesium For Welding
It's crucial to clean and prepare the joint before welding. It goes without saying that you must clean the casting from oil perfectly and any other contaminants on its surface.
Use acetone to wipe the part clean. Afterward, use a carbide burr with a die grinder to remove the magnesium oxide around the joint area and to prepare a nice groove inside the casting crack, if you are repairing a cracked casting. You can also use an angle grinder with a wheel that won't load up when grinding magnesium, but carbide burrs work the best. Just make sure your carbide is coarse.
Since most magnesium welding jobs are actually casting repairs, you'll often have to grind away cracked metal and rebuild the lost material with welding. Basically, you'll melt the filler rod into a casting shape to fill the missing void that you carved out. Afterward, the part will be machined again and be like new.
Photo by @tig_happens
TIG Welding Magnesium
We highly recommend using a TIG welding process to weld magnesium. Of course, you can also use a MIG welding process and other welding methods like resistance, spot, flash, seam, and oxy-fuel welding. However, the TIG welding method works best for most manual welding jobs because it provides the best arc visibility, heat input control, and welding with alternating current.
Since magnesium has an oxide layer on its surface, like aluminum, it's highly beneficial to use AC TIG welding. The alternating current oscillates between DCEP and DCEN to simultaneously achieve oxide removal and penetration. Of course, you need to use a high frequency arc start to reduce any possible contamination, since magnesium is a sensitive metal.
Source: https://melezy.com/electrode-polarity-welding-difference-dcen-dcep-ac/
TIG welders like the YesWelder CT2050 and the YesWelder TIG250P AC/DC should be your choice. They support high frequency arc ignition and AC TIG welding. In addition, they can weld using a pulsed TIG welding process to help you narrow the arc cone just right and focus the temperature input into the cracked groove you are trying to repair. Since magnesium conducts heat rapidly, just like aluminum, you'll need to focus your arc on the joint to provide the necessary fusion.
YesWelder FIRSTESS CT2050 Powerful 7-in-1 Welder & Cutter
You may benefit from preheating the thick parts to about 300F. But, if you are welding thick parts, consider getting a TIG welder with high amperage output. Our YesWelder TIG250P AC/DC can output 250A at 60% duty cycle, letting you weld moderate thickness for a prolonged period of time. But be careful not to input too much heat, either. Excess heat can lead to cracks and embrittlement in the heat affected zone. You should only use enough amps to get the puddle going when welding magnesium, not more.
Shielding Gas Selection
If you must weld very thick magnesium castings, it may be helpful to use 100% helium as a shielding gas because it amplifies the arc's ionization potential and improves heat input. In other words, helium helps you squeeze every bit of energy coming out of your welder. However, many welding professionals do not recommend using pure helium for welding magnesium because it may input too much heat into the joint. So, if possible, make a test on a scrap piece before hooking up a straight helium tank to your TIG setup.
Source: Ionization potential Ei of various gases (www.chemglobe.org) (in increasing order of Ei, (†) metal), (&) inert gases).
For most magnesium welding jobs, you'll do best with a 50/50 argon/helium shielding gas mix. Argon helps to stabilize the arc, and you'll want that arc stabilization, considering how zinc in magnesium alloys reacts to welding. On the other hand, TIG welding magnesium requires a tight arc, so if you use 100% helium, you may lose some arc stability provided by argon.
Filler Metal Selection
The four most commonly used filler metals to weld magnesium alloys are ER AZ61A, ER AZ101A, ER AZ92A, and ER EZ33A. You can buy these as MIG spooled wires if MIG welding, or as TIG welding rods for the TIG welding process.
The table below summarizes the filler metal selection when welding magnesium castings, which is what most magnesium welding jobs require.
Filler Metal Type | Suitable Casting Alloys |
ER AZ101A | AZ92A-T6, for aluminum alloys, for joining HK31A, HZ32A to any other casting alloy |
ER AZ92A | AZ91C-T6, AZ92A-T6, for Aluminum alloys |
ER EZ33A | EZ33A, HK31A, HZ32A to themselves or to each other |
The AZ101A welding rod is the most popular choice and works quite well for welding magnesium castings where no welding procedure is provided. So, if you are hired to repair a casting, but there is no welding specification sheet, or the client doesn't know which magnesium alloy casting is made from, using the AZ101A filler rod is safest. The AZ101 contains 10% aluminum. As a result, it enriches the weld pool with aluminum without introducing a high amount of zinc, which helps prevent cracking.
Don't forget to clean off the oxides from the filler wire. Magnesium really loves oxygen. So, if your filler metal wires package was opened some time ago, you'll have to clean the oxides from the wire.
Oxidized filler wire
Source: https://www.youtube.com/watch?v=ElT5qmUyagU
Tungsten Electrode Selection
Use pure tungsten (green) , zirconated tungsten (white), or thoriated (red) tungsten electrodes to TIG weld magnesium. If you use alternating current, as you should, green and white tungsten are your best bet.
Pure Tungsten Electrode (Green, WP) | YesWelder® TIG Welding Electrode
2% Thoriated Tungsten Electrode (Red,WT20) | YesWelder® TIG Welding Electrode
Travel Angle And Welding Speed
You should bring the filler metal wire as horizontally as you can when welding magnesium in the flat position. Add the filler wire to the edge of the weld puddle, much like when welding aluminum.
The TIG torch should have a slightly leading angle in the direction of your travel. Try to weld quickly to avoid excessive heat input and maintain a steady, consistent travel speed.
Source: https://www.youtube.com/watch?v=ElT5qmUyagU
Conclusion
Welding magnesium does take practice, so we wouldn't recommend jumping the gun and welding a $50,000 worth aircraft casting if this is your first time. Instead, find some scrap magnesium alloy pieces in the junkyard first and try to weld them. See how the puddle behaves and study the arc. It is tricky to keep such a tight TIG arc that you are almost touching the puddle with the tungsten. Luckily, most bad welds can easily be repaired. Just use a carbide burr to eat away the metal and build it up again.
While you can use the MIG welding process, we still recommend the TIG welding method. Most welding professionals repair magnesium castings using AC TIG thanks to its ability to clean oxides and better arc visibility.
Having the skill to weld magnesium alloys can be pretty rewarding too. Few welders can do this. But, magnesium castings are often too expensive to be thrown away over a small crack, surface wear, or a machining mistake. So, if you learn how to conduct such repairs, magnesium welding service can become a new way to obtain highly paid gigs for your welding shop.
Welding up a few magnesium handcycle frames.
Photo by @rda_fabrication
👏 You may be interested in:
- How To TIG Weld Stainless Steel
- How to get the strongest flux-core weld
- How To Weld Aluminum - MIG, TIG, And Stick Welding Explained
📩 Hey! What type of blog content would you like to see from us? Glad to hear from you!